Alice Liu Guards Quality with Professionalism
She is a "steel magnolia" on the quality front line, safeguarding the excellence of every product with her professionalism and meticulousness. She is also the "anchor" in the team, driving the continuous improvement of quality with her wisdom and tenacity. As part of women’s history month, we conducted an exclusive interview with Alice Liu, Quality Manager of Oliver Medical Packaging, to hear how she does it.
Introduction
Alice Liu
Quality Manager of Oliver Medical Packaging, China Region
Alice Liu joined Oliver in 2015. She graduated from Beijing University of Technology and holds an MBA degree from East China University of Science and Technology. As the Quality Manager of Oliver Healthcare Packaging's China Region and as a member of the Medical Device Packaging Professional Committee of the China Medical Device Industry Association, she has over a decade of experience in the medical device industry. At Oliver she is responsible for identifying regulatory requirements for medical device packaging, determining and implementing testing methods, and monitoring the overall quality operation for the company. Alice has published several articles related to sterile medical device packaging materials and testing in professional publications such as Medical Device Packaging Information. She has also led the formulation of the group standard "Determination of Leakage of Non - breathable Packaging or Breathable Flexible Barrier Materials by Dye Penetration Method".
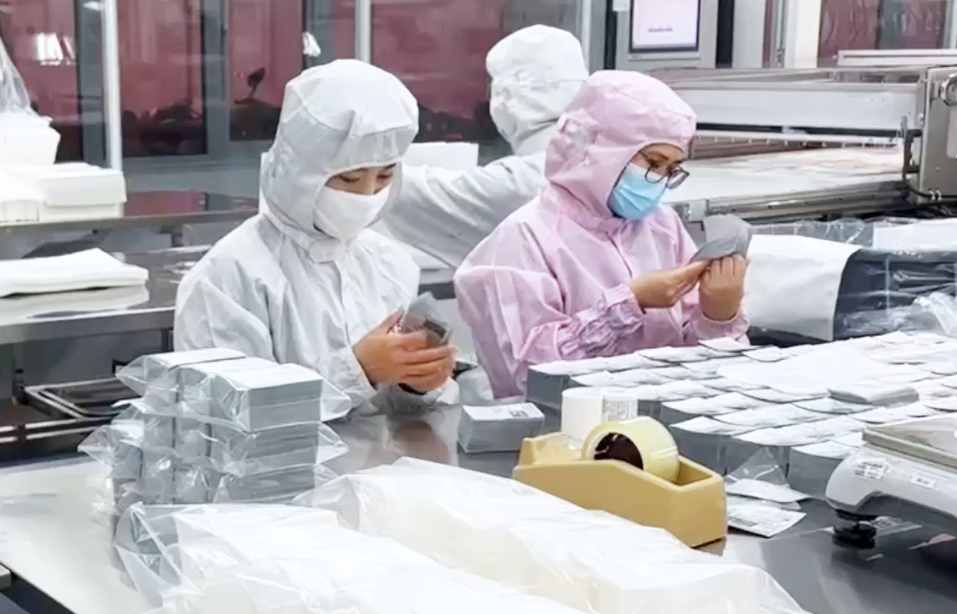
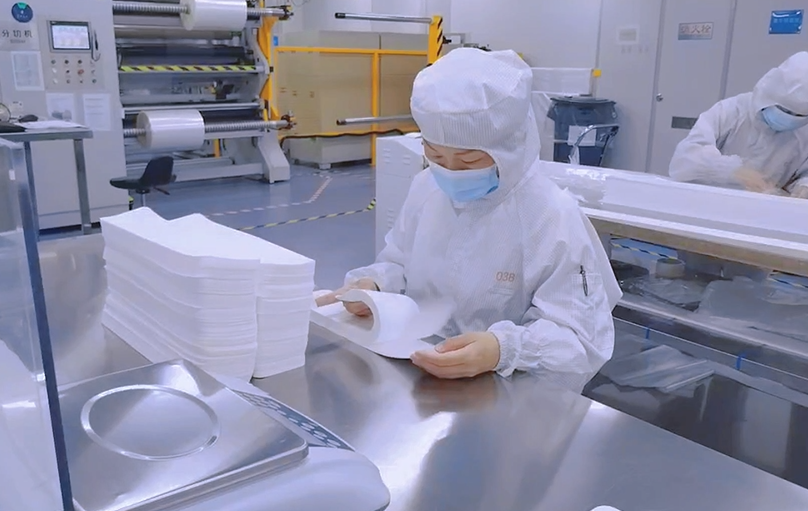
Please briefly introduce yourself, your professional experience, and your main responsibilities at Oliver.
I started my journey in the quality field in the fall of 2004. I was enthusiastic and excited for the rigorous work ahead. I joined a Taiwanese company initially as a quality engineer, then advanced to supervisor, and then finally to department head during my time there.
But time flies! This is now my 11th year at Oliver. I participated in the construction of the company's Suzhou factory. When this facility opened it made Oliver the first packaging enterprise in the medical packaging industry to have a dynamic Class 10,000 production environment. I was responsible for verifying all relevant production equipment and product formulas for Oliver. I’ve also helped establish the only microbiology laboratory at Oliver, globally. Additionally, I led the formulation of the group standard "Determination of Leakage of Non - breathable Packaging or Non - breathable Flexible Barrier Materials by Dye Penetration Method", filling the gap in China’s domestic standards for dye penetration testing of non - breathable materials. Over the past 11 years, I have witnessed the growth of both Oliver and the industry.
How does Oliver control and manage product quality?
How do you ensure the importance of quality is part of your company’s culture?
I believe in prevention first and always being on the lookout for continuous improvement opportunities. It’s important that you integrate quality management and risk management throughout the entire life cycle of a product. A company must establish a complete ISO 13485:2016 quality management system and achieve the unity of knowledge and action by doing as you say and writing as you do.
It’s also important to create a working environment where all employees participate in quality management. Everyone cares about the quality of their own work and does their job well. It is also important to be continuously promoting process improvement projects. Finally, we regularly carry out quality training to integrate the importance of quality into every action of daily work. Through these measures, our company's product quality has always remained at the leading level in the industry.