Flexographic vs. Digital Printing for Medical Packaging
Today, medical packaging faces challenges to be more sustainable, smaller, more cost-effective, all while maintaining the stringent regulations around the text, imagery, and literature that is printed on the package. The materials used in medical packaging are, in many cases, not the most straight forward to print on. We often joke that Tyvek is like printing on the surface of the moon. The non-woven, non-uniform surface creates a challenge for all printing formats. As the printing and packaging industries evolve so do the printing capabilities. In the last couple of years, there has been a rise in interest when it comes to digital printing. With more printing, packaging, and material options to consider, which form of printing is right for your company?
To guide this question, we’re going to walk through some of the differences between flexographic printing, which is the most common print process in the packaging industry today, and digital printing, the most quickly growing process for the packaging industry.
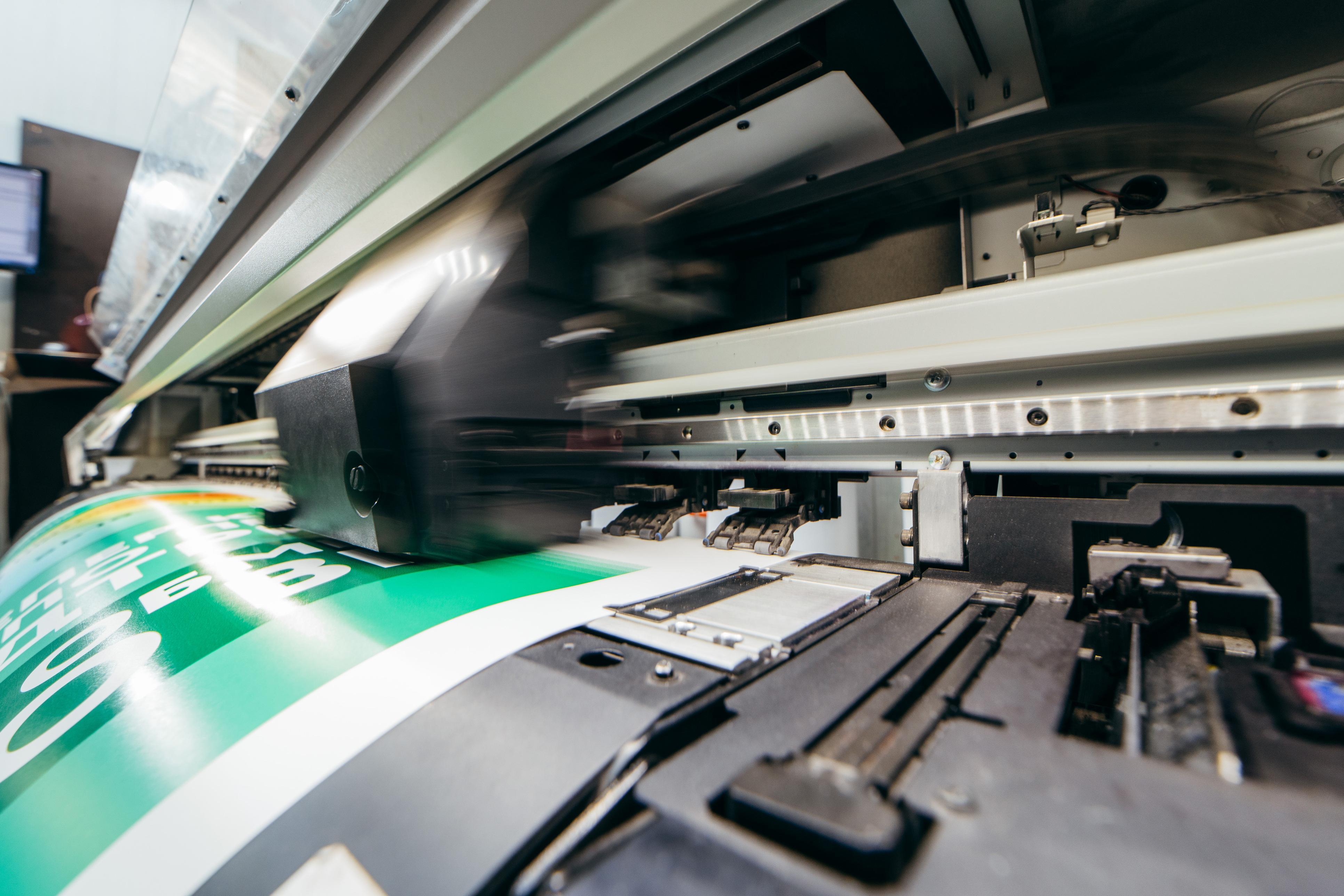
Flexographic printing
The flexographic printing process as we know it today began to take shape in the early 1900’s and is the predominant printing format in the food and medical packaging industries. Flexographic printing gets its name from the flexible photopolymer plate used to transfer ink onto a substrate. The best comparison is to think of a rubber stamp, the surface on the printing plate is raised where it is intended to transfer the ink to the substrate. However, instead of stamping, it is applied using a rotary process through which ink is transferred from a metering roller to the plate, and then onto the substrate.
Printing plates are one of the major differences between flexographic and digital print processes. With every print SKU, physical tooling is required, which is an upfront investment and not something that can be easily changed in the middle of a press run. With printing plates, the ink is applied one color at a time. This means every color used requires a different plate, time to set up, impress, and then ink up. The more colors, the more complex the run and of course, a greater impact to upfront cost. While setup may sound cumbersome, flexographic printing becomes more efficient as volume increases, and is capable of providing a very high-quality print.
Digital printing
Digital printing is an emerging technology in our industry and historically, the medical packaging industry has been slow to adopt new technologies—rightfully so. Everything is done with patient safety in mind; due diligence is critical. I would consider digital printing to still be in a growth and emergence phase because the technology itself is still improving. With that said, digital printing is finding its way into more applications for packaging products and processes every year.
Instead of buying tooling to transfer ink into a pattern or design, a digital inkjet press relies on a digital file to communicate graphic information. With no tooling and tooling lead time requirements, this can be a big advantage in terms of upfront cost and the time it takes to turnaround a product. Because there are no plates required and very minimal set up, digital printing is a very effective process for short runs or prototypes. Ink is transferred onto the substrate through jet nozzles. These jets release microscopic droplets onto the substrate. Droplets are measured in picolitres, that’s one trillionth of a liter! These droplets combine in a pattern to make up the photographs and graphics we see printed on the material surface. Similar to flexo, digital inkjet machines print one color at a time to make up the artwork.
Compared to flexographic printing, digital has a higher capability for variable data printing because it is much easier to change artwork from run to run, or even mid-run. Say for example, you have an order of 500 lids and you need an individual lot code on each lid, you can do this easily with digital inkjet. With flexography you would need to change the tool for each unique print.
Lastly, it’s also fair to say that a digital press will produce less waste in short runs. This is due to precise ink application and less set-up scrap needs. It simply takes less material to produce an initial image and to calibrate to the customer’s specification.
Printing Colors
Digital inkjet relies heavily on process CMYK printing to achieve the finished image. Process printing combines several ink layers to create the target color. The standard digital press uses a four-color process system using cyan (C), magenta (M), yellow (Y), black (K), more commonly known as CMYK. Every target color will always be made using some combination of these four. With digital printing, there is very little room for spot color printing capability, because colors cannot be easily interchanged within a digital print head. Spot color printing, in contrast to CMYK, is the process of applying one pre-formulated ink to achieve the intended color, instead of combining multiple inks in process.
With flexography, colors can be easily interchanged within the machine. This means that CMYK printing is possible, spot color printing is possible, and a combination of the two is also possible, provided there are enough print heads in the machine to accommodate each color. With medical packaging graphics and medical packaging materials, spot color printing offers some of the most vibrant, and cost-effective graphics that flexo can achieve, and is therefore most commonly found on Oliver products.
Which printing method is right for your product?
Both printing options are excellent choices for high resolution graphics on medical packaging. Some of the biggest considerations when identifying the appropriate process are time to press, run lengths, and total volume requirements. Digital will be more economical for short runs. However, digital inkjet ink is more expensive, and press speeds are slower, so there is a higher per unit cost compared to flexographic printing. If looking to complete a large volume run, flexographic printing becomes the cost-effective solution.
If graphic requirements include halftone images like a photograph, digital inkjet may be the preferred option for image consistency on rough surfaces such as Tyvek or uncoated papers. If graphics include unique spot colors such as metallics or pastels, flexography would be the preferred option for color accuracy.
Finally, Digital presses today accommodate narrow to mid-sized web widths. If you are looking for wide-web roll stock, digital may not be an option for you. As previously mentioned, digital inkjet is an emerging technology, and first generation wide-web digital inkjet presses are making their way to the market. We will continue to see advancements in digital printing for the packaging industry, and as the technology scales, expect to see a reduction in consumable costs as well.