Thermoforming Packaging Solutions and Optimization Options
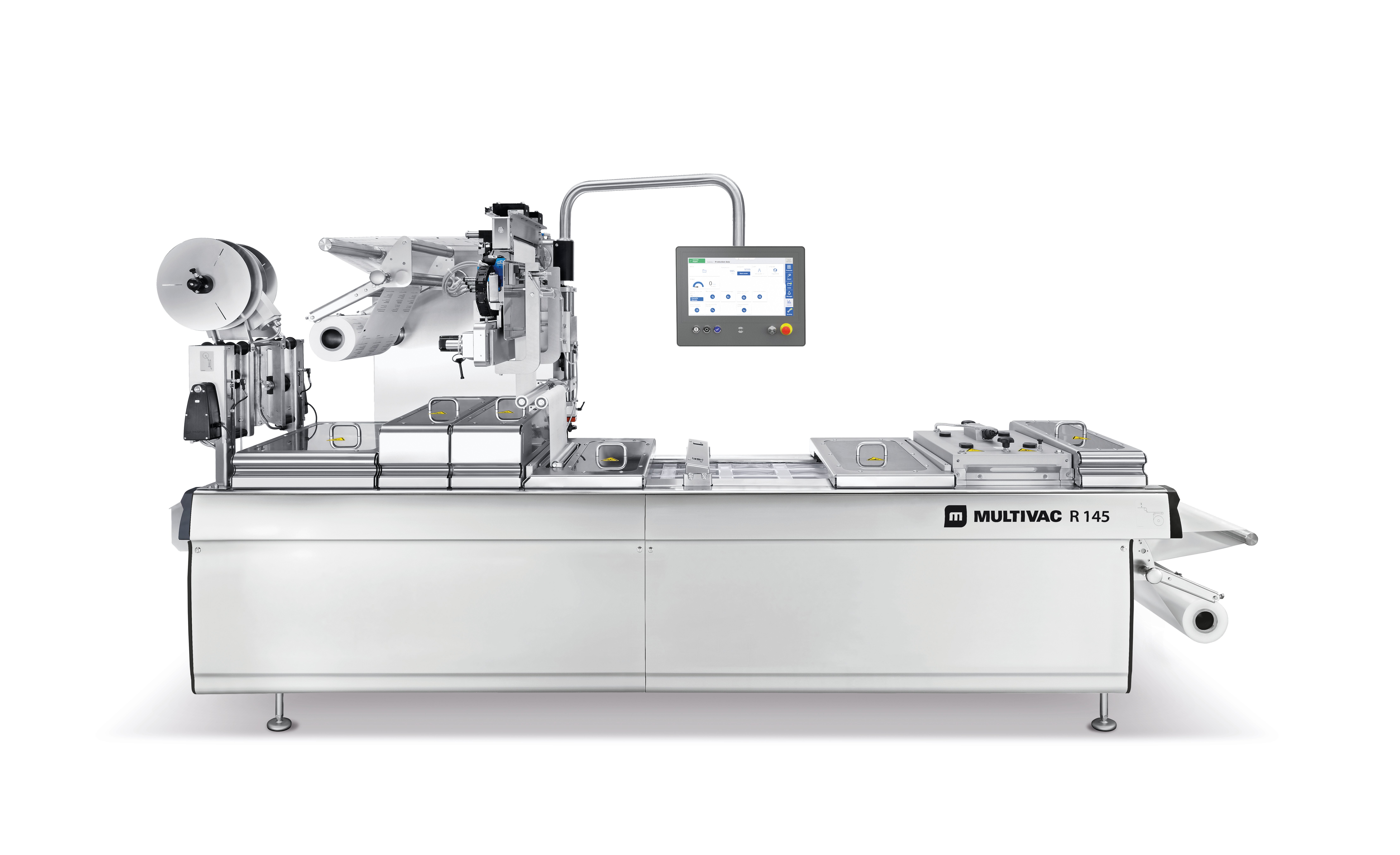
In the field of medical and pharmaceutical packaging, understanding the basics of thermoforming processes is essential when you are developing your packaging. This blog article provides an educational overview of thermoform packaging technologies, explores the thermoforming process, and looks at how you can optimize your packaging to ensure it is both high-quality and efficient.
Understanding Thermoforming Packaging
Thermoforming packaging machines produce packages by forming the bottom film with three key aspects: heat, pressure, and time. From there, it seals the bottom film with the top film and lastly, it cuts the material into individual packages.
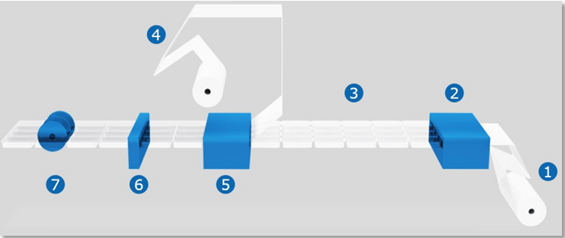
Unwinding the Bottom Film
Forming Station
Loading Area
Unwinding the Top Film
Sealing Station
Cutting Stations
Key Parameters in Thermoforming
There are three parameters that are crucial for the thermoforming process: time, temperature, and pressure. These parameters must be carefully monitored and adjusted to ensure optimal packaging quality. For instance, the heating and forming time depend on the film thickness, while the heating temperature varies with different film materials. The pressure build-up-time is related to the volume of the die.
Optimization Options
Once you have a clear understanding of the thermoforming process and know the key parameters it takes to create your packaging, you can start investigating different ways of optimizing the packaging.
These are a few examples of opportunities to improve both: packaging design and sustainability:
- Package Design: Designs can be modified to improve the stability by adding features such as ribs and grooves, or changing the corner shape. Material consumption can also be reduced by thoughtfully shaping the package. You can look to reduce the partition widths between the packs, the sealing flange, or edge trim width.
- Material Alternatives: Different material structures have different properties and based on your product’s needs you might be able to downgauge or select an easier to recycle structure. If you are interested in learning more about his, check out this PackTalk article: Exploring Forming Films: When and How Do You Choose a Forming Film?
- Film Distribution: Thermoforming with plug-assist and explosion forming are two effective methods for optimizing film distribution. Both techniques allow deeper forming with a thinner packaging film. This contributes to more efficient and sustainable packaging by reducing material consumption without compromising the quality and integrity of the package.
In conclusion, knowing the thermoforming packaging process is essential for developing high-quality, efficient, and sustainable packaging solutions in the medical and pharmaceutical industries. By understanding the key parameters and steps involved, optimization options such as improved package design, material alternatives, and utilizing advanced techniques like plug-assist and explosion forming, companies can significantly enhance their packaging efficiency and reduce material consumption. If you are interested in learning more about these topics, you can listen to the webinar: Mastering Forming Films: Expert Insights and Best Practices.
Work with MULTIVAC and Oliver
Looking for a new packaging concept or to optimize your existing packaging solution? Reach out to MULTIVAC or Oliver to learn more.