When Will the Supply Chain Recover?
If you remember the summer and fall of 2020, when people were still adjusting to their new post-COVID-19 “normal”, you remember how hard it was to find certain things. People were spending a lot more time at home, which caused a surge in demand for things like patio furniture, and outdoor heating units. Buying behavior was focused on making homes more comfortable, and manufacturers answered that call. But as COVID became more manageable, people adjusted their lifestyles and preferences. They learned to live with COVID, started taking vacations again, and stayed home less. Demand preferences changed quickly, but it took the supply side longer to adjust. As a result, big box stores now have an abundance of patio furniture and heating units simply because the need (or demand) is lower than it once was.
The same basic principles of supply and demand imbalance are at work in the world of healthcare packaging, but there are significant differences between how COVID impacted the consumer goods industry and the wide-scale disruption we have observed within healthcare packaging.
You may have heard that material availability is improving across our industry, and it is. While we are encouraged, it’s important to understand that this is just the beginning of a process that will improve slowly over time.
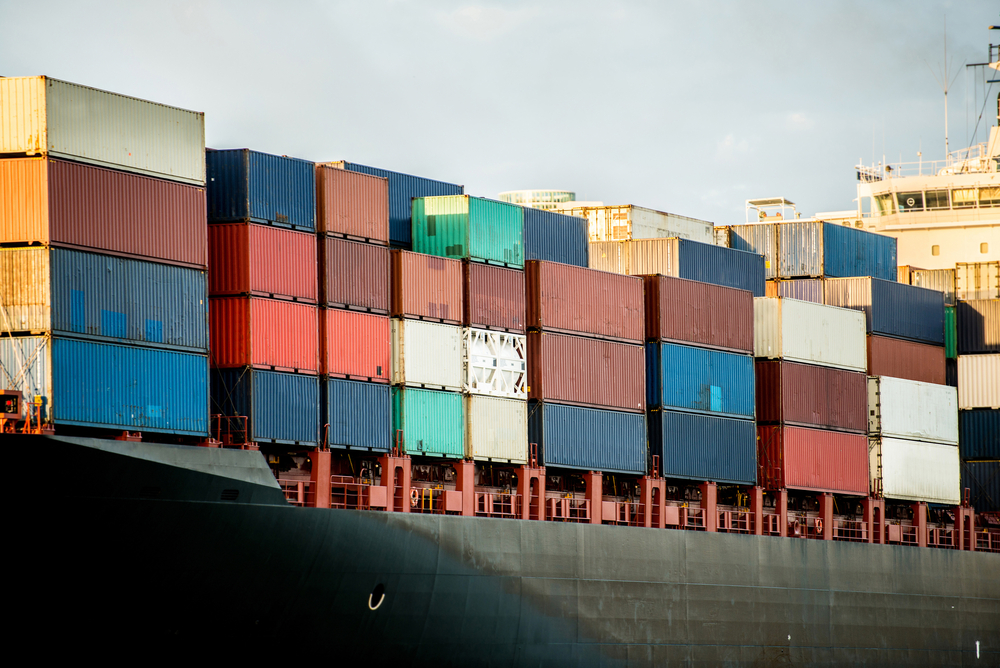
The supply chain for healthcare packaging is complicated, and when one link in the medical supply chain is suffering—such as constrained supply of input ingredients—the full process suffers. We have had significant issues within multiple aspects of the supply chain over the past two and a half years, amplifying disruption to the entire system.
There are four main components of the supply network, and issues in any of these can cause supply problems
-
Demand patterns: the overall order quantity and mix of products needed by the market
-
Input material supply: the availability of materials needed to produce sterile and high barrier packaging
-
Converting throughput: the capacity of labor and equipment available to convert input materials into finished goods
-
Logistics network: the availability and efficiency of transportation for both raw materials and finished goods
Each area has experienced significant challenges between March 2020 and today. Some of the problems, such as issues within the logistics network, were directly attributable to COVID. Other issues, including constraints with some important resins, were due to contemporaneous problems that were unrelated to COVID, but had a dramatic effect on the availability of important input materials at a time when demand was already elevated.
From a demand perspective, COVID created huge demand changes for medical devices and related equipment, essentially overnight. Demand for personal protective equipment (PPE) increased dramatically during the first 18 months of the pandemic. Materials that would normally be available for other applications were severely constrained because they were prioritized for PPE. At the same time, the mix of necessary medical devices changed dramatically, with items related to “elective” procedures plummeting while items needed for acute care and vaccinations skyrocketed. Many patients deferred all but their most critical healthcare needs until after vaccines were widely available, which created a large procedure backlog that will take years to clear. The net result was a slack in demand for elective procedures for roughly 12 months from the onset of the pandemic, followed by a dramatic surge in demand.
The supply of input materials was initially constrained due to the massive demand for PPE, which required a large amount of material that uses high density polyethylene (HDPE). Diverting input materials to PPE limited the amount of material available for other important applications and constrained the supply of sterile barrier packaging. Furthermore, in February 2021, roughly the same time demand for elective medical procedures was recovering, there was a “deep freeze” in Texas that caused a huge disruption to many facilities that produce polyethylene resins. Shortages of polyethylene resins from qualified suppliers resulted in severe constraints in input materials for more than a year. Demand remained very strong during this time, resulting in material rationing and the accumulation of significant order backlogs.
For our part, Oliver has been doing everything we can to add equipment to expand capacity to satisfy demand as materials become more readily available. This is easier said than done, as the specialized equipment for manufacturing healthcare packaging relies on materials such as steel, which also suffered from extended lead times and became expensive. Automated manufacturing equipment also requires microprocessors, which were unavailable and resulted in significant delays in the deliveries of new equipment.
Last but not least, the healthcare packaging supply chain depends on the logistics network to bring our input ingredients to us, as well as ship materials between facilities and to our customer sites around the world. The global disruptions in trucking, rail networks, and ports & container shipments were crippling in many ways, and resulted in additional, unpredictable delays on top of the other challenges that existed in the market. When production schedules are running “just in time” due to material constraints, any delayed shipment of input materials forces the entire production schedule to be reworked.
The good news is that we are seeing improvements across all aspects of the supply chain. Input materials are more readily available. The logistics network is slowly recovering. We’ve made massive investments to increase our throughput to improve service levels as supply and demand equilibrate. But like most companies in healthcare packaging, Oliver continues to work through an accumulated backlog. Clearing this backlog will require all components of the supply chain to be functioning properly for the next 6 –12 months.