Your Medical Packaging Print Testing Questions Answered
When it comes to printing and medical packaging, it’s important to test and understand what you are looking for to ensure the quality of your product is maintained. After all, the print on medical packaging almost always plays an important role in patient and user safety with disclaimers, device instructions, and pertinent manufacturer information. In fact, did you know that it is considered mislabeling in the medical packaging world if the information on your packaging is illegible?
We recently sat down with Dr. Rong, print and material professor at Cal Poly, to better understand what types of print testing can and should be done to ensure a high-quality medical packaging product. Read our interview below:
Can you start by telling us a little bit about yourself?
What types of printing tests are done on medical packaging?
In my experience, there are two different types of testing related to printing. The first being for function and the second being for appearance. Both are performed at the R&D stage before production and provide valuable information for the design team.
For function related print testing you’re typically looking for abrasion or rub resistance. Ensuring that during shipping, the printed image or text on the packaging is not removed. This test is done following ASTM standard D5264, Standard Practice for Abrasion Resistance of Printed Materials by the Sutherland Rub Tester. It is tested under controlled conditions to evaluate the ability of how a printed surface resists smearing and scuffing. Mostly this is visually examined, although sometimes you might measure the change of color density before and after the test to determine the quality. This test is typically performed as an R&D tool to compare the relative performance of one set of materials over another.
The second type of testing we typically do is appearance testing for both resolution and legibility. This is especially important for medical packaging where there are limited printable surfaces for legal statements and instructions on the packaging which require the print of small fonts and fine illustrations. This test focuses on how plates, inks, and substrates will impact the resolution of the graphics or logos and the legibility of text. It visually examines the finest recognizable weight of the lines and font sizes in both positive and reverse forms. Typically, this testing is just done with a visual check, as there are no standards associated with it. This does mean that the results of this type of testing are subjective.
Lastly, with appearance, color accuracy is the other testing option. The same color can be printed differently depending on the type of printing process, ink, and substrate you select to use. Typically, a spectrophotometer will allow you to evaluate the color of your print and determine the color differences between the reference color and the printed one. This is often used to compare the specified brand color and spot colors to the print version and evaluate the accuracy of color reproduction.
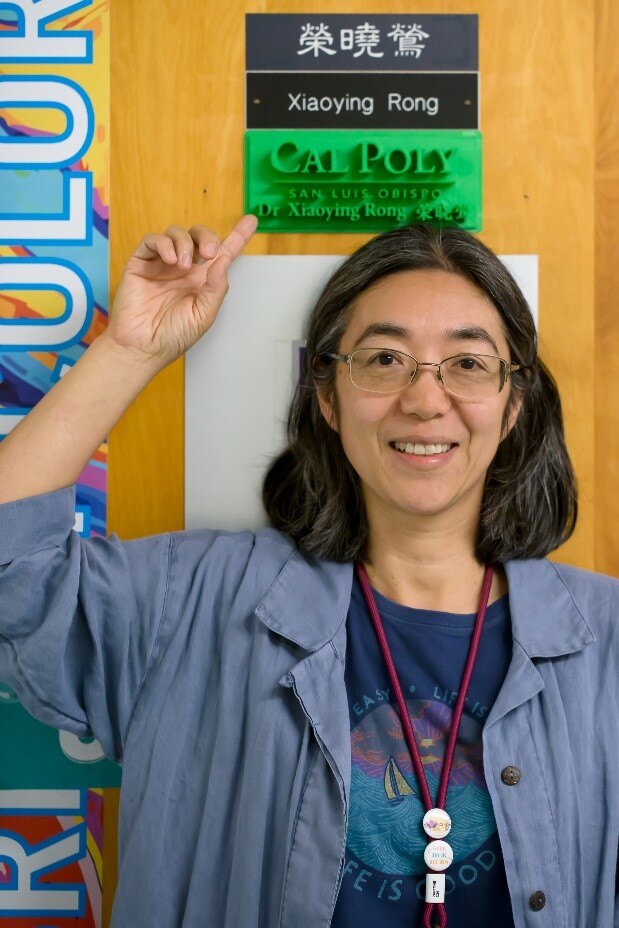
Why would a company test their printing? And for a given test type, when do they test it?
Testing your printing ensures, as a company, that you maintain good quality throughout the life cycle of your product. The abrasion resistance test is related to the substrate and ink combination, where legibility and resolution testing is relevant to printing technology, print press, and plate technology used to print the packaging. It is a combined result of printing process, ink, and substrate. I recommend that this be identified through well-defined tests at your product’s development stage. By doing this testing before starting your packaging design and print production, you can be confident with your product’s print quality with the ink, substrate, and printing conditions you have. You can also trust the quality of your product will be maintained when it finally makes it into the hands of your end user or customer.
Is print testing always done?
From a development standpoint, yes, it is almost always done at the development stage. But when you are changing printing presses, substrates, or inks, you’ll want to do it again. Packaging companies that do not have in-house printing will have their packaging printers do an internal test so they know exactly what they can do and cannot do.
How often does print testing need to take place?
Rub testing should take place during the development stage before the product is on the press. Resolution testing should be determined before designing the packaging to inform the designers what are the smallest fonts and thinnest lines can be reliably produced with the materials and print conditions. Once it is running on the press, the printers will intermittently pull samples throughout the printing process to check for registration, color density or spectro data, pinholes, and other defects to make sure there are no quality issues during production. A rub test can be conducted again for quality assessment.
What additional tests do you recommend outside of standard?
Testing is typically related to what type of product you have for your end users. For example, you might need to test beyond just appearance to understand the toxicity of the ink if that is a concern of your packaging.
Which print methods or ink tend to work better for medical device packaging?
It really depends—currently my experience working with Oliver is that we are looking at a lot of water-based inks and inks with ingredients that can pass the toxicity test for medical applications, since most of medical device packaging is in direct contact with a device. We’ve seen that flexo and lithography are the two main processes used for medical device packaging printing. Once you move away from the primary packaging or direct contact packaging, such as the secondary packaging and tertiary packaging, you likely will have more options for the printing process and material choices. Processes with UV ink printing can usually be explored. In my experience, the closer you are to your product, the more the focus is about what inks are safest, which tends to be very restrictive and from very limited suppliers. When you move to the outer layers of packaging and further from your product, more ingredients can be used in the ink formulation as toxicity is usually not an issue.
What are your thoughts on innovation in this space? What do you see coming to the forefront vs. what is the current standard?
The consumer packaging industry is moving towards bringing more interactive experiences to the users. A great example of this is QR codes combined with augmented reality (AR) content. If regulation were to allow medical packaging to do this in the future, it could be very interesting. Imagine if you could scan a QR code and provide an experience where the patient or doctor can review how to use the device through augmented reality. Another trend we’re seeing in the consumer space is more color, smaller batches, and more personalized packaging. This though can be costly for medical device packaging because it requires more printing stations if all the colors are printed as spot colors. It is also challenging if you only need a small quantity of your packaging as the current production methods are most cost effective when printing in large quantities. While the digital printing technologies advance with more safe materials and become more versatile on various substrates, we will see more color come into medical device packaging design, bringing cost-effective packaging solutions to small LOT devices, and providing personalized packaging to serve the individual needs of users.